The next major step after finishing the cab for Colorado Central #10 is fabricating the domes. I had some Kemtron domes, but they weren’t a close enough match to the prototype, so I decided to turn my own.
I’m certainly aware of the many advances in technology that are used in the hobby, especially 3-D printing. So, why do I spend the time and effort turning domes from brass rod? The answer is simple: I enjoy it. It’s immensely satisfying to see the shape of the dome slowly emerge from the brass rod.
This type of turning is one of the most basic lathe operations and a good way to learn to use your lathe. Because there are no critical tolerances involved, turning domes is a great way to start.
In the late 1960s, I bought a Unimat SL and went to the local community college to sign up for a course in basic machining. When I told the instructor I had just purchased a Unimat, he called it a toy — so I left. That was the extent of my formal training as a machinist.
The Unimat SL was a great way to learn basic miniature machining techniques and very forgiving of my mistakes. Although I now have both a Sherline lathe and Sherline vertical milling machine, I still have my old Unimat permanently set up as a precision miniature drill press.
There are many different lathe tools for different operations, but I just use a few basic ones for turning domes. I do initial cutting with right and left rough cutters, fine work with a finishing tool, and use a parting tool to cut the finished dome from the bar stock.
This article briefly introduces the tools, initial set-up of a lathe, and establishing the basic shape of the dome. In Part 7 in the January/February 2021 Gazette I will complete describing how I turn domes.
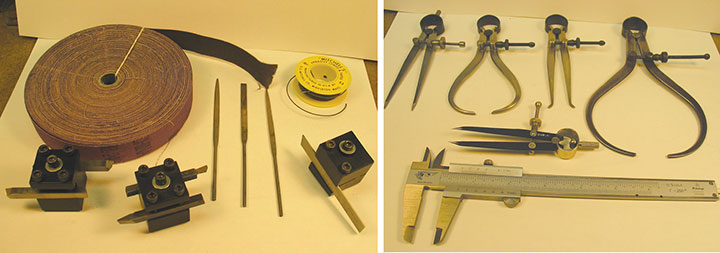
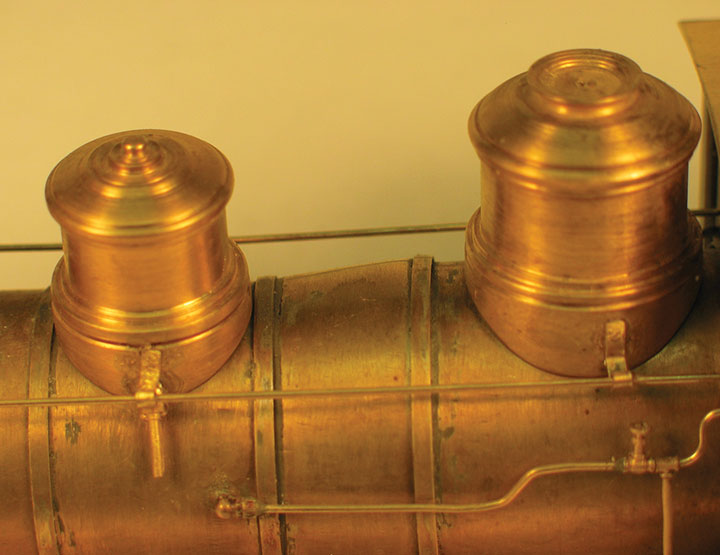
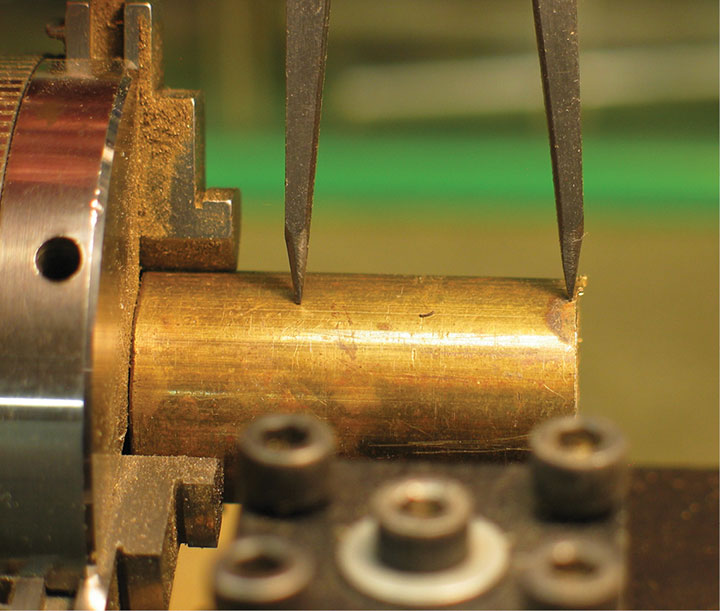
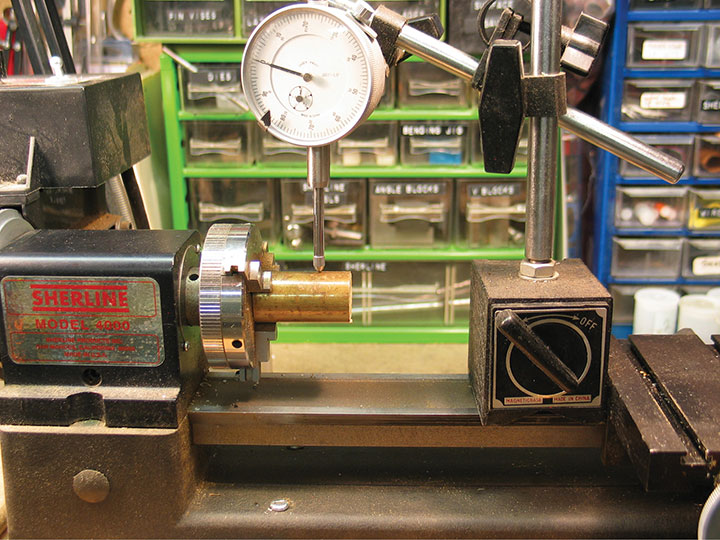
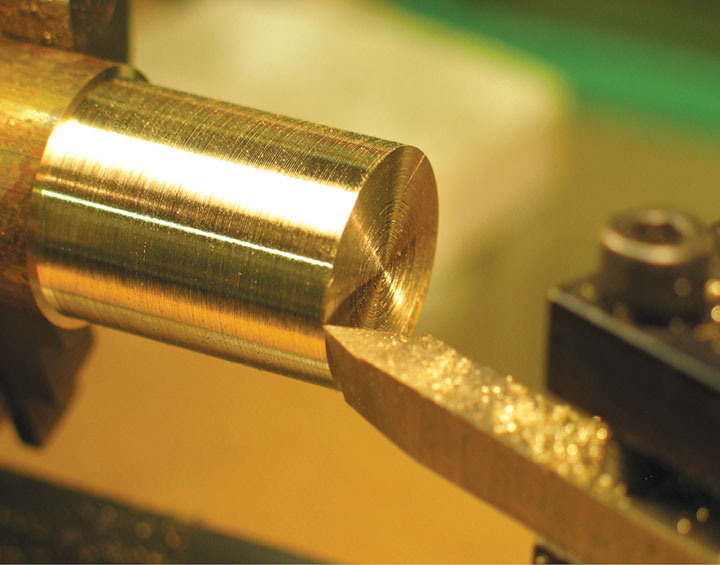
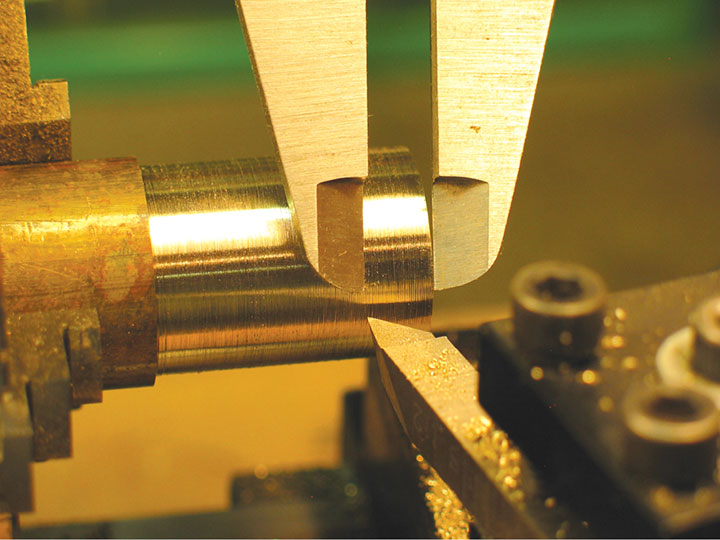
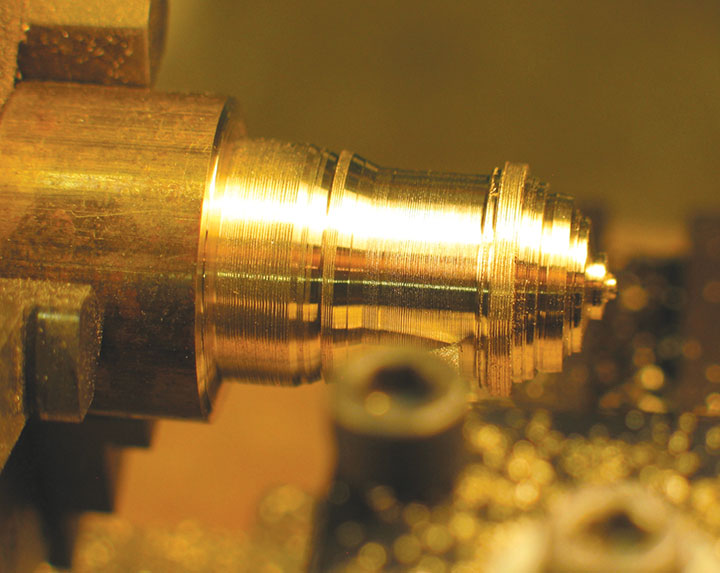